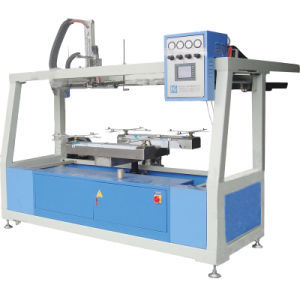
The Many Uses of Reciprocating Pumps and Compressors
If you work in any production plant or factory, you know for a fact that the bulk of the operations and production rely on the use of heavy machinery. As much as possible, companies want to make sure that everything is running smoothly, especially their machines. A delay in production can significantly affect the performance, productivity, and operations of a company. Proper machine monitoring is vital to its overall function. With the right tools, companies will know beforehand if the machine requires repair before they suffer from serious damage that requires replacement from this website.
There are various machines and technologies that companies use to monitor the proper function of their machines. For rotating machines, the use of vibration sensors is most common as well as reciprocating pumps and compressors. Reciprocating pumps come with a built-in automatic sensor test diagnostics and verification. These sensors are essential for guaranteed machine monitoring point precision, accuracy, and system reliability. The use of this monitoring sensor is also effective for detecting excessive machine cashing temperature and vibration. You can do different process measurements using a reciprocating compressor, yet the most cost-effective will have to be impact severity and crankcase frame vibration. These pumps and compressors are also crucial to abnormal foundation vibration and process equipment housing detection.
Vibration analysis using reciprocating pumps and compressors offers comprehensive spectra information on any presence of mechanical failure and faults. With the use of integral reciprocating pumps and compressors, you can expect uniquely designed algorithms that help to detect mechanical looseness or impact severity in compression cylinders. They also aid in the detection of any abnormalities in the combustion gas engine detonation present in power cylinders. Be sure to click here for more info!
The use of reciprocating pumps and compressors also means getting accurate condition monitoring diagnostics and process equipment protection. The compressor cylinder valves are among the most common maintenance parts present in any reciprocating compressor. The most expensive part of a reciprocating compressor will have to be its crankshaft.
Using quality reciprocating pumps and compressors allows the overall monitoring of vibrations in machinery. You can also use band-pass filters according to your specifications to make vibration monitoring suitable to your requirements such as the application and type of process equipment you use. See this video at https://www.youtube.com/watch?v=UgUMPfMdg8A for more info about machines.
When you use these reciprocating pumps, you get one-of-a-kind vibration signatures in the x, y, and z spectra for every monitoring point you have established. You can then compare these signatures to previous records or any similar machines that you have for you to make sure that your machines are reliable and performing to their exact specifications. You can view website to get more info about these reciprocating pumps and compressors.